Sikaflex®-252
Good adhesion on a variety of substrates
Suitable even for high dynamic loads
Good gap-filling properties
Overview
Product advantages
- Good adhesion on a variety of substrates
- Suitable even for high dynamic loads
- Good gap-filling properties
- Recoatable
- Vibration damping
- Electrically non-conductive
Application
Sikaflex®-252 is suitable for assemblies that are exposed to dynamic loads. Suitable substrates are wood, metals, especially aluminium (also anodised), sheet steel (also phosphated, chromated or galvanised), metal primers and lacquers (two-component systems), ceramic materials and plastics. Observe manufacturer’s recommendations before using Sikaflex®-252 on materials at risk of stress cracking. Pre-tests must be carried out with original materials to avoid stress cracking. This product is only suitable for experienced users. To ensure adhesion and material compatibility, preliminary tests must be carried out with original materials under the relevant conditions.
Product details
Product features
Chemical base | 1-component polyurethane | |
Colour (CQP001-1) | White, grey, black | |
Curing mechanism | Moisture-curing | |
Density before curing | Depending on colour | 1.2 kg/l |
Stability | Good | |
Application temperature | Environment | 10 to 35 °C |
Skin formation time (CQP019-1) | 40 minutes | |
Through-curing speed (CQP049-1) | See diagram 1 | |
Hardness Shore A (CQP023-1 / ISO 7619-1) | 50 | |
Tensile strength (CQP036-1 / ISO 527) | 3 MPa | |
Elongation at break (CQP036-1 / ISO 527) | 400 % | |
Tear resistance (CQP045-1 / ISO 34) | 7 N/mm | |
Operating temperature (CQP513-1) | -40 to 90 °C | |
4 Hours | 130 °C | |
1 Hour | 150 °C | |
Durability (CQP016-1) | Cartridge / Bag | 12 Months |
Technical information
Sikaflex®-252 cures by reaction with air humidity. At low temperatures, the water content of the air is lower and the cross-linking reaction is somewhat slower.
Sikaflex®-252 is generally resistant to fresh water, sea water, dilute acids and dilute alkalis; temporarily resistant to fuels, mineral oils, vegetable and animal fats and oils; not resistant to organic acids, glycol, concentrated mineral acids and alkalis or solvents.
Application
Surface pretreatment
The adhesive surfaces must be clean, dry and free from grease, oil, dust and impurities. The surface preparation depends on the specific condition of the substrate and is decisive for a durable bond. Instructions for surface pretreatment can be found in the current Sika® pretreatment table. The information contained there is based on experience and must always be verified by preliminary tests with original materials.
Processing
Sikaflex®-252 can be processed between 10 °C and 35 °C (climate and product). Changes in reactivity and application properties must be taken into account. The optimum temperature for substrate and adhesive is between 15 °C and 25 °C.
Note viscosity increase at cool temperatures. For easy application, heat the adhesive to room temperature. For an even adhesive layer thickness, it is recommended to apply the adhesive in the form of a triangular bead (see figure 1).
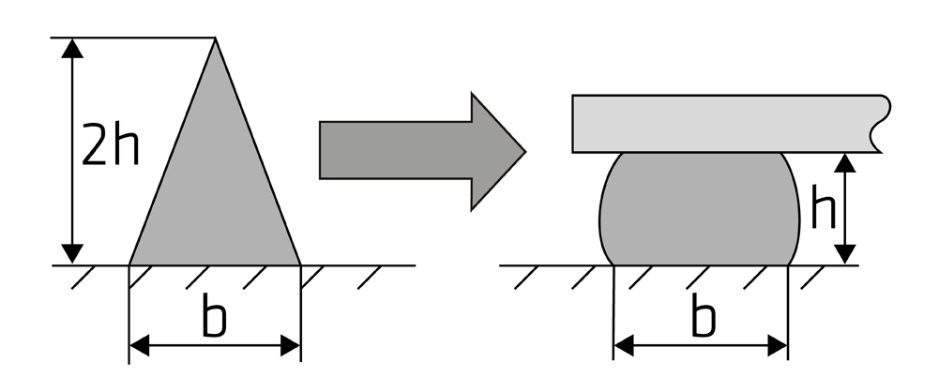
Apply Sikaflex®-252 with a suitable cartridge/bag gun or pump unit. The skin formation time is significantly shorter in hot and humid climates. Always join components within the skin forming time. Do not press after a skin has formed.
Smoothing
Smoothing must be carried out before the adhesive forms a skin. For smoothing we recommend Sika® smoothing agent N. Other smoothing agents must be checked for their suitability.
Removal
Not cured Sikaflex®-252 can be removed from tools and equipment with Sika® Remover-208 or other suitable solvents. Cured material can only be removed mechanically. Hands/skin must be washed immediately with suitable cleaning cloths (e.g. Sika® Handclean) or industrial hand cleaners and water. Do not use solvents on the skin!